Lug Analysis Validation
In Section 9.6 of the Air Force Stress Analysis Manual, an example is provided for an axially loaded lug. The male lug strength, female lug strength, and double shear joint strength are calculated. This validation case follows the Air Force example to ensure consistent results between the Air Force Manual and MechaniCalc's Lug Analysis calculator.
Male Lugs and Bushings
The inputs for the male lug, per the input table, are specified below:
Geometry:
D | = | 1 in | hole diameter |
e | = | 1.5 in | edge distance (hole center to edge of lug) |
a | = | 1 in | distance (edge of hole to edge of lug) |
w | = | 3 in | width |
t2 | = | 0.75 in | thickness |
Material Properties: 7075-T651 Plate
Sty | = | 66,000 psi | tensile yield strength |
Stu | = | 77,000 psi | tensile ultimate strength |
E | = | 10.3 x 106 psi | elastic modulus |
εu | = | 0.06 | ultimate strain |
Comparison Summary
A summary of the male lug results calculated in the Air Force Manual versus those calculated in MechaniCalc's Lug Analysis calculator is provided below. It can be seen that the results are essentially equivalent. Any differences are due to slight variations in determining the \(K\) coefficients from the charts, or are due to rounding errors.
Air Force Manual | MechaniCalc Lug Calculator | |
---|---|---|
Lug Bearing Strength | 77,000 lbf | 77,060 lbf |
Lug Net-Section Tension Strength | 100,485 lbf | 101,466 lbf |
Bushing Bearing Strength | 44,000 lbf | 44,010 lbf |
Combined Lug-Bushing Design Strength | 44,000 lbf | 44,010 lbf |
Lug Bearing Strength
The male lug bearing strength as calculated in the Air Force Manual is:
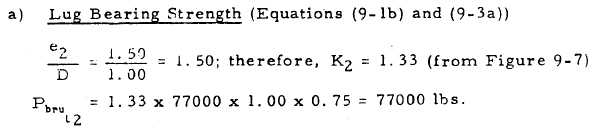
The results from the Lug Analysis calculator are shown below. The predicted bearing strength is just slightly below that calculated in the Air Force Manual (28,440 lbf vs. 28,600 lbf) due to a slightly lower \( K_{axial} \) value read off of the figure (1.45 vs. 1.46). The strength values are within 0.56%.
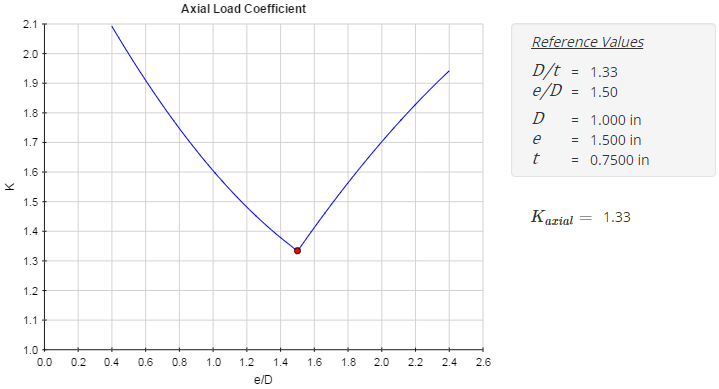
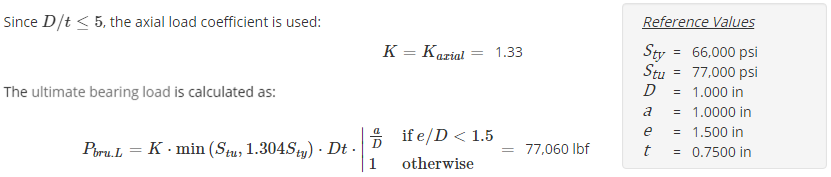
Lug Net-Section Tension Strength
The male lug net-section tension strength as calculated in the Air Force Manual is:
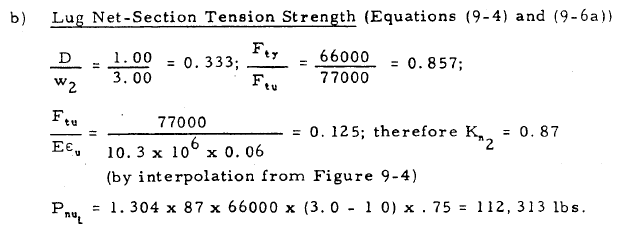
NOTE: The final equation above is incorrect, and the corrected value is \(P_{nu.L} = 100,485 \text{ lbf} \). A full explanation is given below.
In the equation for \(P_{nu.L}\) above, the incorrect equation was used (9-6b vs. 9-6a). The relevant equations from the Air Force Manual are shown below:
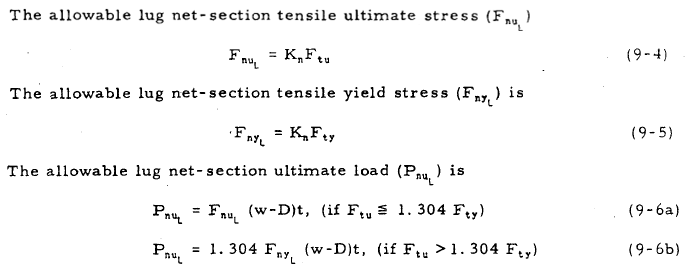
If \( F_{tu} \le 1.304 F_{ty} \), then Equation 9-6a should be used, otherwise Equation 9-6b should be used.
\( F_{tu} = 77000 \text{ psi} \) \( 1.304 F_{ty} = 86100 \text{ psi} \) |
→ | \( F_{tu} \lt 1.304 F_{ty} \) |
Since in this case \( F_{tu} \lt 1.304 F_{ty} \), Equation 9-6a should be used. Although the solution in the example stated that Equation 9-6a was used, in reality 9-6b was used. The correction for the example is:
$$ \begin{eqnarray} P_{nu.L} &=& F_{nu.L} (w-D) t \\ &=& K_n F_{tu} (w-D) t \\ &=& 0.87 \cdot 77000 \cdot (3.0 - 1.0) \cdot 0.75 \\ &=& 100,485 \text{ lbf} \end{eqnarray} $$The results from the Lug Analysis calculator are shown below:
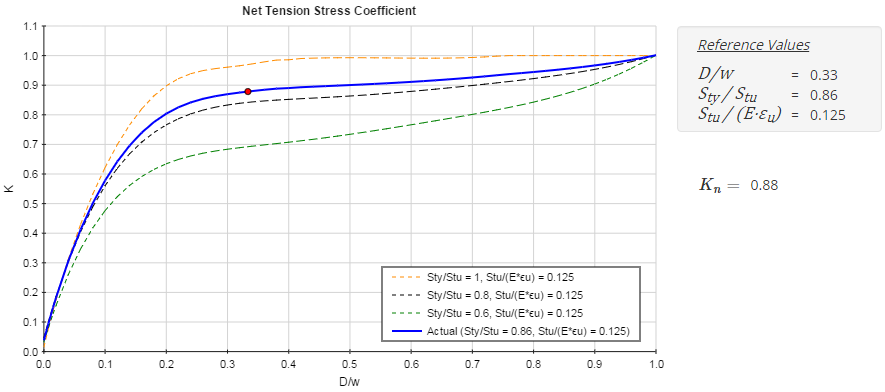

Lug Design Strength
The male lug design strength as calculated in the Air Force Manual is:
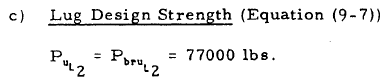
MechaniCalc's Lug Analysis calculator does not determine a design strength until the bushing bearing strength has also been calculated (in the next step).
Bushing Bearing Strength
The male bushing bearing strength as calculated in the Air Force Manual is:

The results from the Lug Analysis calculator are shown below. The predicted bearing strength is equivalent to the value calculated in the Air Force Manual (with the only differences being attributable to rounding on the part of the Air Force Manual):
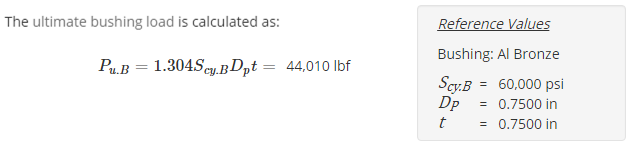
Combined Lug-Bushing Design Strength
The combined male lug-bushing design strength as calculated in the Air Force Manual is:

The results from the Lug Analysis calculator are shown below. The predicted strength is equivalent to the value calculated in the Air Force Manual:
